THAT MAKES
THE DIFFERENCE
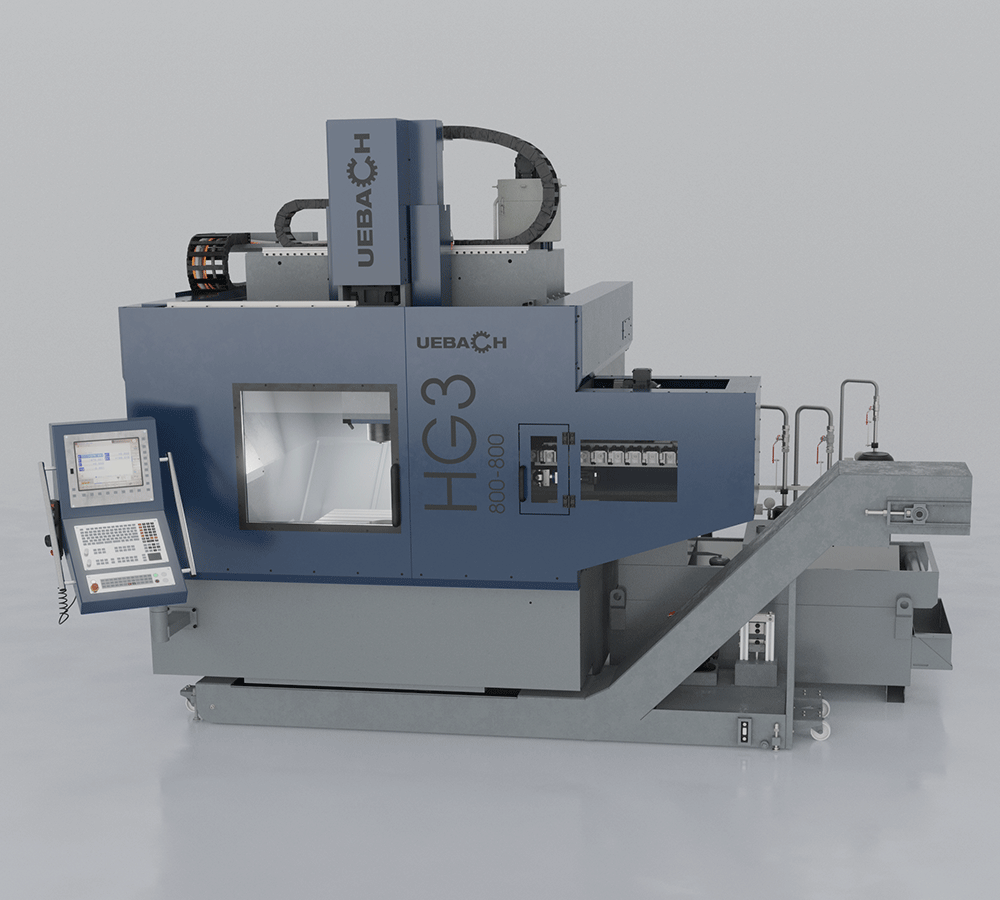
HG3-800-800
Number of axes | 3 |
---|---|
Travel distances | |
X (mm) | 800 |
Y (mm) | 800 |
Z (mm) | 500 |
Main spindle speed (RPM) | 12000 |
Position tolerance TP (mm) | 0,006 |
-
- Characteristics -
- Geometric stability and vibration-damping structure due to gantry design
- High machining performance due to robust design
- High dynamics achievied through powerful drives
- Optimal chip removal thanks to steep walls in the machining area and generously dimensioned chip conveyor
- Machine can be easily loaded with a crane due to the far-retracting gantry
- No guiding, measuring systems, or ball screws in the machining area
- Compact milling spindle unit (no motor spindle)
- Easy accessibility for service tasks
- Good accessibility to the machine table due to the overhanging guideways
- Quick and easy alignment of the machine due to monoblock design
-
- Assistance for Self Help -
Frequently, you can perform maintenance, repairs, or service tasks on your own. Detailed repair and service manuals will assist you in executing these tasks professionally. This concept was already taken into account during the design of the HG3 machine type, resulting in a logical and straightforward structure. If desired, our qualified service personnel are ready to provide support.
Moreover, when it comes to procuring spare parts, operating supplies, or any other materials, we guarantee the most cost-effective and prompt solutions. You can choose to rely on our extensive inventory or source directly from the manufacturer as per your preference.
-
- Optional Equipment -
- Tool magazine for holding 30 tool (further tool places on request)
- High-pressure coolant system standard: 20 bar, optional: 40 bar
- Collision monitoring / Brankamp 2-channel
- Camera for indoor surveillance
- Triple machine vices with various clamping elements
- 3D touch probe / Heidenhain
- Handwheel
- Suction system
THAT MAKES THE DIFFERENCE
HG3-1200-1000
- Geometric stability and vibration-damping structure thanks to the portal design
- High cutting performance due to robust construction
- High dynamics thanks to powerful drives
- Optimum chip removal through steep walls in the machining area and generous
dimensioned chip conveyor - The machine can be optimally loaded with a crane thanks to the retracting portal
- No guide, measuring systems or ball screws in the machining area
- Compact milling spindle unit (no motor spindle)
- Easy accessibility for service work
- Easy access to the machine table thanks to the overhanging guideway
- Quick and easy alignment of the machine thanks to the monoblock design
- Quadruple guided Z-axis
HG3-800-800
- Geometric stability and vibration-damping structure due to gantry design
- High machining performance due to robust design
- High dynamics achievied through powerful drives
- Optimal chip removal thanks to steep walls in the machining area and generously dimensioned chip conveyor
- Machine can be easily loaded with a crane due to the far-retracting gantry
- No guiding, measuring systems, or ball screws in the machining area
- Compact milling spindle unit (no motor spindle)
- Easy accessibility for service tasks
- Good accessibility to the machine table due to the overhanging guideways
- Quick and easy alignment of the machine due to monoblock design
ASSISTANCE FOR SELF-HELP instead of expensive service technicians.
Frequently service tasks, maintenance, or repairs can be carried out mostly independently. Detailed service and repair instructions help you execute these tasks correctly. This concept was already taken into account during the desgin of the HG3 machine type, resulting in a logical and uncomplicated design. If desired, our qualified service staff can provide support.
When it comes to procuring spare parts, consumables, or other materials, we guarantee the most cost-effective and fastest solution. You have the option to utilize our extensive inventory or procure directly from the manufacturer.
Workspace
Travel XYZ axis | 1200 / 1000 / 800 mm |
---|---|
Distance spindle fixed table min. / max. | 1000 / 200 mm |
staring table
clamping surface table | 1300 x 1000 mm |
---|---|
9 T-slots according to DIN 650 in X-direction | 18 H7 |
2 alignment grooves in the X direction | 18 H7 |
table load max. | 4000 kg |
Feed drive XYZ axis
AC servo drives maintenance-free, digital | |
---|---|
Rapid traverse speed XYZ axis | 20 m/min |
Feed force XYZ axis at 40% ED | 20,5 kN |
main spindle drive
milling spindle | |
---|---|
tool holder | SK50 DIN 69 817 Big |
Drive power at S1 | 50 kW |
Speed range, stepless max. | 1-8000 U/min |
Torque at 25% ED | 690 Nm |
tool magazine
Magazine slots, 1 plate | 32 |
---|---|
Tool diameter when fully loaded max. | 100 |
Tool diameter with free adjacent spaces max. | 160 |
tool length max. | 300 |
tool weight max. | 10 kg |
Measuring system XYZ, direct
Position tolerance TP according to VDI/DGQ 3441 | ≤ 0,007 mm |
---|---|
machine weight approx. | 25.000 kg |
CNC Control | TNC 640 Heidenhain |
Workspace
Travel distance XYZ axis | 800 / 800 / 500 mm |
---|---|
Distance spindle fixed table min. / max. | 150 / 650 mm |
Fixed table
Clamping surface table | 800 x 800 mm |
---|---|
8 T-slots according to DIN 650 in the X direction | 18 H7 |
Table capacity max. | 2000 kg |
Feed drive XYZ axis | 25 m/min |
Main spindle drive
Milling spindle | direct-drive with CTS |
---|---|
Tool holder | SK40 DIN 69 871 |
Drive power at S1 100% | 17,5 kW |
Speed range, stepless max. | 1-12000 rpm |
Torque at S6 40% | 192 Nm |
Tool magazine
Magazine slots, 1 chain | 30 pcs. (more on request) |
---|---|
Tool diameter when fully loaded max. | 80 mm |
Tool diameter with free adjacent spaces max. | 125 mm |
Tool length max. | 300 mm |
Tool weight max. | 8 kg |
Total load max. | 150 kg |
Measuring system XYZ, direct
Position tolerance TP according to VDI/DGQ 3441 | ≤ 0,006 mm |
---|---|
Machine weight approx. | 11.000 kg |
CNC Control | TNC 640 Heidenhain / Siemens |
Coolant device
Tank capacity | 600 Liter |
---|---|
Coolant pressure CTS | 20 Bar |
External cooling | 4 nozzles |
Milling air | available |
Dimensions
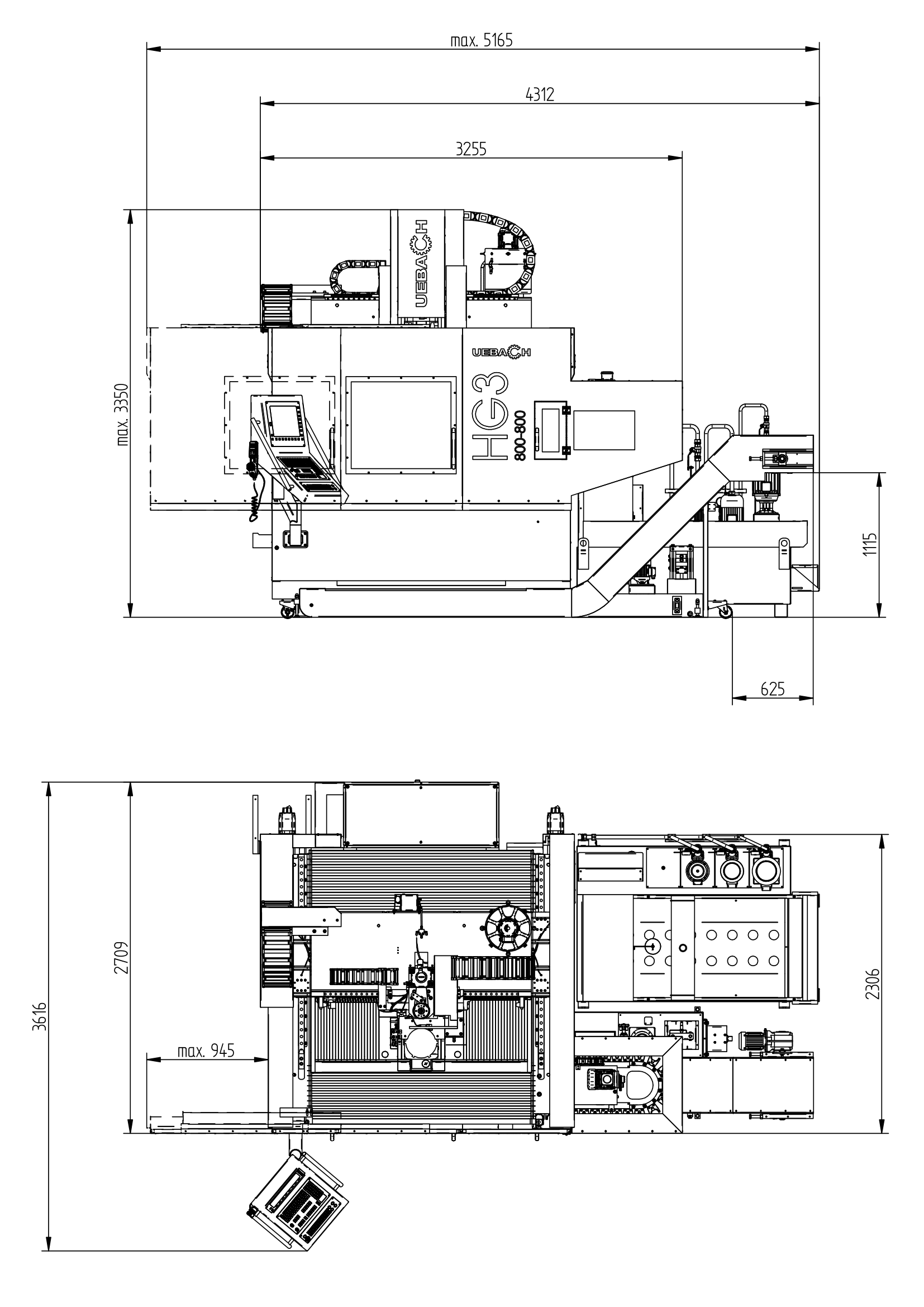
Bildtitel
Kollisionsüberwachung / Brankamp 2-Kanal
ButtonBildtitel
3D-Tastsystem / Heidenhain
Button
OPTIONAL EQUIPMENT.
- Milling spindle with spindle speed max. 5,000 rpm, 8,000 rpm
- Tool magazine for holding either 10, 20, 32 or 36 tools
▸ further tool places on request - High-pressure coolant system standard: 20 bar, optional: 40 bar
- Collision monitoring / Brankamp 2-channel
- Camera for indoor surveillance
- Triple machine vices with various clamping elements
- 3D touch probe / Heidenhain
- handwheel
- suction system
Bildtitel
Kollisionsüberwachung / Brankamp 2-Kanal
ButtonBildtitel
3D-Tastsystem / Heidenhain
Button
OPTIONAL EQUIPMENT.
- Tool magazine for holding 30 tools
▸ further tool places on request - High-pressure coolant system standard: 20 bar, optional: 40 bar
- Collision monitoring / Brankamp 2-channel
- Camera for indoor surveillance
- Triple machine vices with various clamping elements
- 3D touch probe / Heidenhain
- Handwheel
- Suction system
your direct
contact person
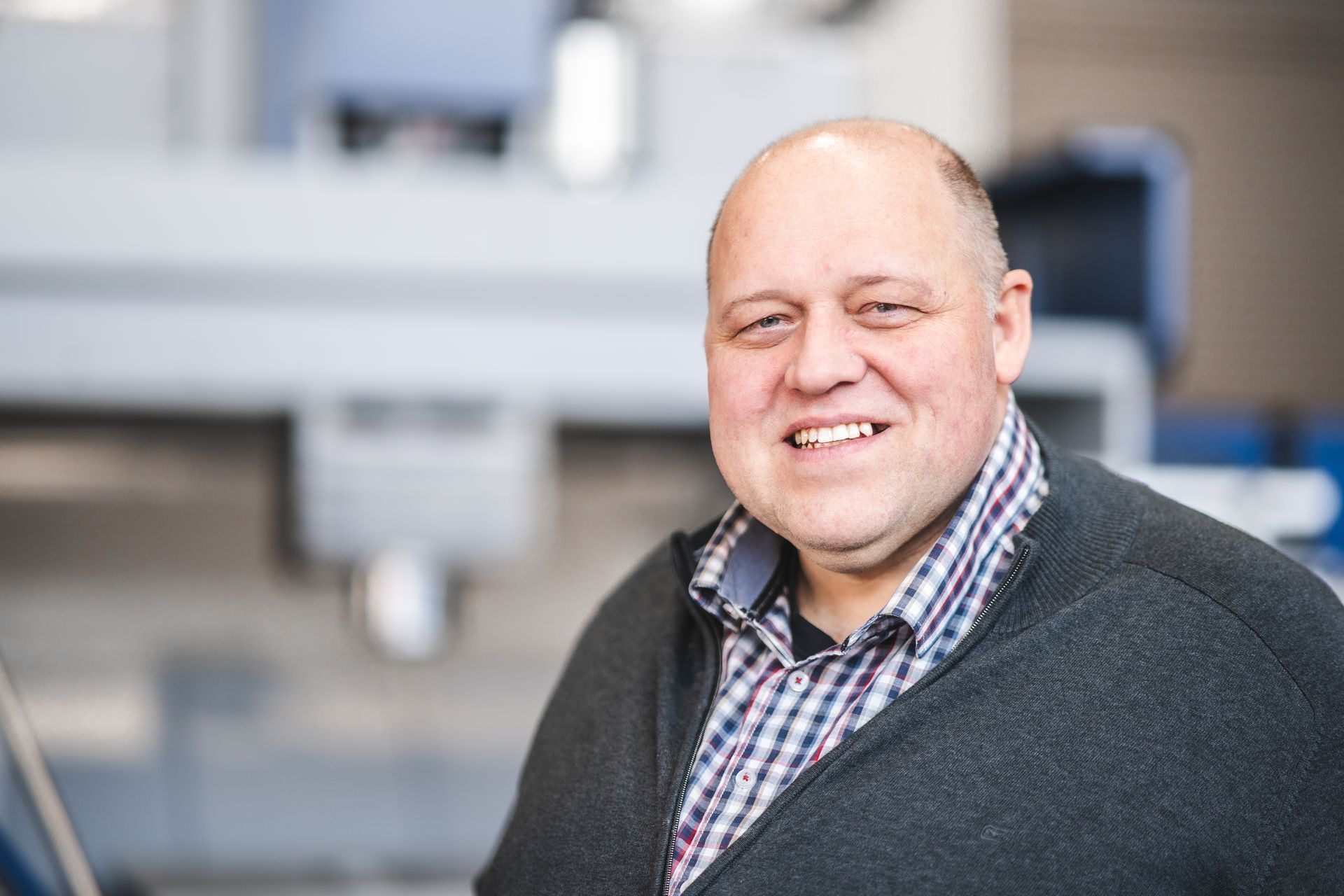
LUTZ UEBACH
CEO
Phone: 02745 9311-16
Fax: 02745 9311-30
Mail: info@maschinenbau-uebach.de
LUTZ UEBACH
CEO
Phone: 02745 9311-16
Fax: 02745 9311-30
Mail: info@maschinenbau-uebach.de